Converting Fischer-Tropsch waxes into transport fuels involves catalytic processes like hydrocracking and dewaxing. By using catalysts such as nickel-molybdenum, you can break down heavy waxes into lighter, usable components. This method not only enhances cold-flow properties but also produces high-performance diesel with low-sulfur content. The resulting fuels typically have a high cetane number, making them a viable alternative to conventional petroleum products. Keep going to discover more about optimizing these processes and their benefits.
Key Takeaways
- Fischer-Tropsch (FT) waxes can be effectively converted into transport fuels through hydrocracking, enhancing their usability and marketability.
- The hydrocracking process reduces heavy wax fractions into lighter, more desirable liquid fuels suitable for transportation.
- Utilizing catalysts, such as nickel-molybdenum, during hydrocracking improves conversion efficiency and fuel quality.
- Optimizing process conditions, including temperature and pressure, is crucial for maximizing yield and minimizing undesirable byproducts.
- FT-derived diesel from upgraded waxes typically features high cetane numbers and low sulfur content, ensuring excellent performance and environmental benefits.
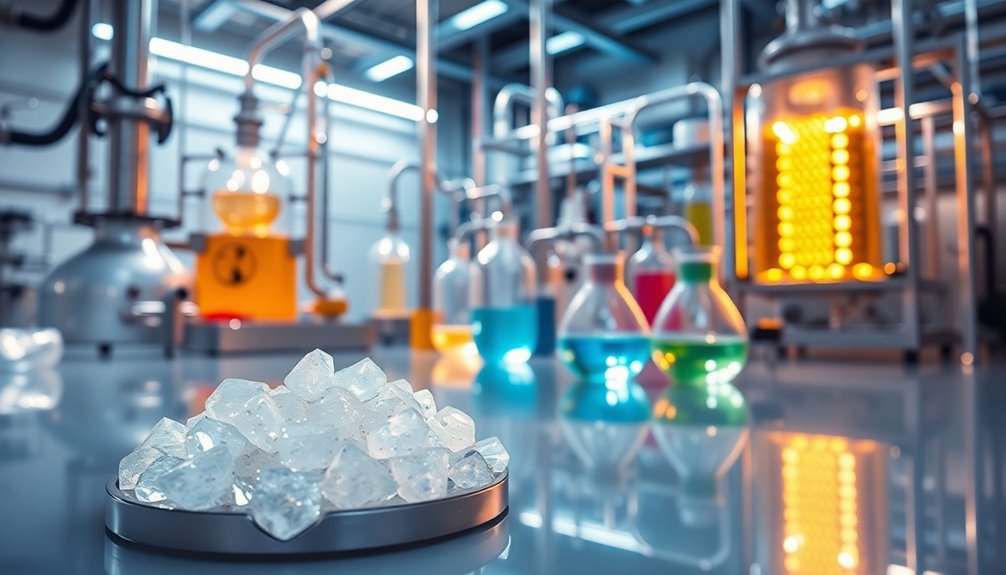
As the world seeks cleaner energy solutions, converting Fischer-Tropsch (FT) waxes into transport fuels offers a promising avenue. The Fischer-Tropsch process effectively converts syngas into liquid hydrocarbons using metal catalysts, primarily cobalt or iron. This process is essential for producing low-sulfur diesel fuel and addressing petroleum supply challenges. Fischer-Tropsch (FT) Process helps monetize traditionally waste products that are often flared, further supporting environmental sustainability.
You'll find that optimizing the FT process for sustainable aviation fuel (SAF) production can significantly reduce carbon emissions, making it an attractive alternative.
Cobalt is the more commonly used catalyst due to its longer lifespan, but iron plays a role as well. To enhance catalyst performance, promoters like rhenium, platinum, and ruthenium can be introduced. Additionally, nickel-molybdenum catalysts are utilized in hydrocracking, which is crucial for upgrading FT waxes into marketable fuels.
Cobalt catalysts offer durability in Fischer-Tropsch processes, enhanced by promoters and nickel-molybdenum for effective hydrocracking.
The choice of catalyst support, such as alumina, silica, or titania, also influences performance, impacting product yield and quality.
When it comes to process conditions, maintaining the optimal temperature range of 150°C to 300°C is key. Pressure levels typically fall between one and several tens of atmospheres to favor the formation of longer hydrocarbon chains. The right H2:CO ratio is vital, especially for cobalt catalysts, which require ratios of 1.8 to 2.1.
While higher temperatures and pressures can speed up reactions, they also increase the risk of undesirable byproducts like methane.
To upgrade FT waxes, hydrocracking is employed to break down heavy fractions into lighter, usable components. This process often requires dewaxing to enhance the cold-flow properties of the resulting diesel fuels.
You'll appreciate that FT-derived diesel typically boasts a high cetane number, often exceeding 70, ensuring excellent performance.
Frequently Asked Questions
What Are Fischer-Tropsch Waxes Used for Besides Transport Fuels?
Fischer-Tropsch waxes have a variety of applications beyond transport fuels.
You can find them in PVC processing as lubricants, improving production efficiency. They enhance hot melt adhesives, coatings, and polishes, providing durability and gloss.
In the rubber industry, they boost wear resistance, while in cosmetics, they offer a smooth texture.
They also serve in food and pharmaceuticals as releasing agents and enhance durability in paper and textiles.
How Does the Catalytic Process Affect Fuel Quality?
The catalytic process significantly affects fuel quality by enhancing properties like stability, yield, and environmental friendliness.
When you use effective catalysts, you're likely to see reduced olefin content and increased isoparaffin levels, which improve fuel stability and performance.
Operating at optimal temperatures and pressures further refines the fuel, reducing impurities.
What Are the Environmental Impacts of This Conversion Process?
The environmental impacts of converting Fischer-Tropsch waxes into transport fuels are significant.
You'll notice reduced greenhouse gas emissions compared to traditional fuels, especially when using renewable feedstocks like biomass. This process also allows for versatile fuel production while improving energy efficiency.
However, keep in mind that water management and catalyst disposal are crucial to minimizing negative effects.
Are There Alternative Methods to Convert Fischer-Tropsch Waxes?
Oh, you thought hydrocracking was the only game in town? Think again!
You've got options like fluid catalytic cracking, which transforms waxes into various products, or steam cracking, perfect for breaking down large hydrocarbons.
Don't forget catalytic reforming, which refines the end products, or even catalytic pyrolysis for those adventurous enough to explore.
Each method brings its unique flair, so you've got plenty of paths to consider for converting Fischer-Tropsch waxes!
What Economic Factors Influence the Viability of This Process?
When considering the economic factors influencing the viability of converting Fischer-Tropsch waxes, you need to focus on plant size, feedstock costs, and catalyst expenses.
Larger facilities reduce production costs, while the availability and price of biomass feedstocks affect profitability.
Additionally, the costs of catalysts and energy inputs play crucial roles.
Market competition, regulatory incentives, and consumer willingness to pay a sustainability premium also significantly impact the economic attractiveness of this process.
Conclusion
In the grand scheme of things, turning Fischer-Tropsch waxes into transport fuels may seem like a minor feat. After all, who needs cleaner fuels when you can just stick to the old ways? Yet, as you explore these catalytic processes, you'll realize it's not just about innovation; it's about necessity. So, while the world spins on its axis, you might just find that these waxes hold the key to a more sustainable future—who knew?